追求技术极致创新的爱旭股份,已率先找到破解隐裂难题的关窍。单面焊接技术、无银金属化涂布工艺、更优的拉力设计,爱旭一套技术创新“组合拳”,极大降低了其N型ABC组件的隐裂风险,有效减少了不可抗力造成的隐裂损失,为组件的高可靠性保驾护航。
摆脱“银依赖”,组件更强韧
“为了光伏行业的可持续发展,去银化是必然道路。”7月25日,中国光伏行业协会主办的“新型光伏金属化产业发展创新论坛”上,国电投新能源科技有限公司首席技术官王伟在演讲中作出上述论断。而爱旭N型ABC组件采用的“无银金属化涂布”技术,正是其抗隐裂性能的重要来源之一,在摆脱传统工艺对银的依赖的同时,与之相伴的隐裂风险也迎刃而解。
长期以来,银都被光伏行业视作不可或缺的电极材料。传统电池工艺在银浆制备过程中掺入玻璃粉,制成的电池栅线与焊点是银和玻璃粉的结合体,结构疏松不够稳定,容易造成隐裂。爱旭N型ABC电池采用自有专利无银技术,以纯金属铜栅绑定硅片,电池韧性和强度都得到了全面提升,抗隐裂能力也随之增强。
此外,传统工艺使用银浆时需经过烧结过程,会对电池硅片晶格造成一定损伤,这也使得本就脆弱的晶硅电池更易出现隐裂现象。而爱旭N型ABC电池采用的无银金属化涂布技术无需经过高温烧结,能够保持硅片晶格完整,降低电池隐裂风险。
不仅如此,爱旭无银金属化涂布设计在提升组件抗隐裂性能的同时,还有效降低了原先高昂的电池用银成本,且确保了原材料的充沛供应。
统计显示,全球范围内光伏行业对银的需求从2020年至今翻了一番,占到白银总需求的20%。摩根士丹利在今年7月的一篇报告中指出,全球白银市场已经连续三年出现供应短缺;银价也随之高歌猛进,今年5月COMEX白银期货价格一度较2024年初涨超30%。
在光伏电池非硅成本中,银浆占比约35%,是非硅成本中占比最高的一项。无银金属化涂布技术不仅是减少隐裂风险的良策,更是光伏行业探索可持续发展的新路。
“一”字型焊接,ABC电池边缘“减负”
正如ABC(全背接触)字面之意,爱旭N型ABC电池栅线均分布在背面,因此有别于传统的“Z”字型串焊,爱旭N型ABC可采用“一”字型焊接技术,即正面无焊带,电池互联的所有焊带均分布在电池片背面,并且位于同一水平面上。
传统的“Z”字型串焊技术中,焊带在电池片上下表面来回穿梭,对电池片的上下表面造成局域压迫,在狭窄的空间内对电池片的边缘施加多点单向压力,增加了隐裂风险,威胁组件的机械可靠性。而爱旭N型ABC组件的“一”字型焊接技术避免了电池片与焊带在间隙处的正反面搭接,这种设计不仅不会对电池片的机械性能造成威胁,反而起到了共面绑定、应力分散的正向作用,降低了转接处的裂片风险,提升了组件的可靠性。
与此同时,爱旭N型ABC组件焊带宽度达到1.2毫米,是市场上其他主流产品的4-6倍,焊接拉力分布更加均匀,远优于竞品。一系列焊接技术的结合应用,使爱旭N型ABC组件可靠性大幅提高,更加游刃有余地应对各类隐裂风险。
“硬”实力经得起考验
爱旭N型ABC组件从技术与设计上攻克了大部分可能造成隐裂的隐患,面对外部冲击的实际表现又如何呢?一旦冲击过大发生隐裂,N型ABC组件相比其他传统组件的发电损失又有多大差异?
为了更直观地展现爱旭N型ABC组件的抗隐裂能力,爱旭专门在SNEC展台上设立了单片电池冲击性能测试,对不同产品的抗冲击性能及受冲击后的电流损失进行对比。实验中,在2公斤1.1米/秒的机械冲击下,TOPCon电池片基本碎裂,电池片从冲击处向四周大面积碎裂开来,电流损失高达44.61%;而同样条件下的N型ABC组件仅在遭受冲击的接触面处发生断裂,电流损失降至16.48%,且涂布电极依然紧密地连接着电池片,并未散乱。
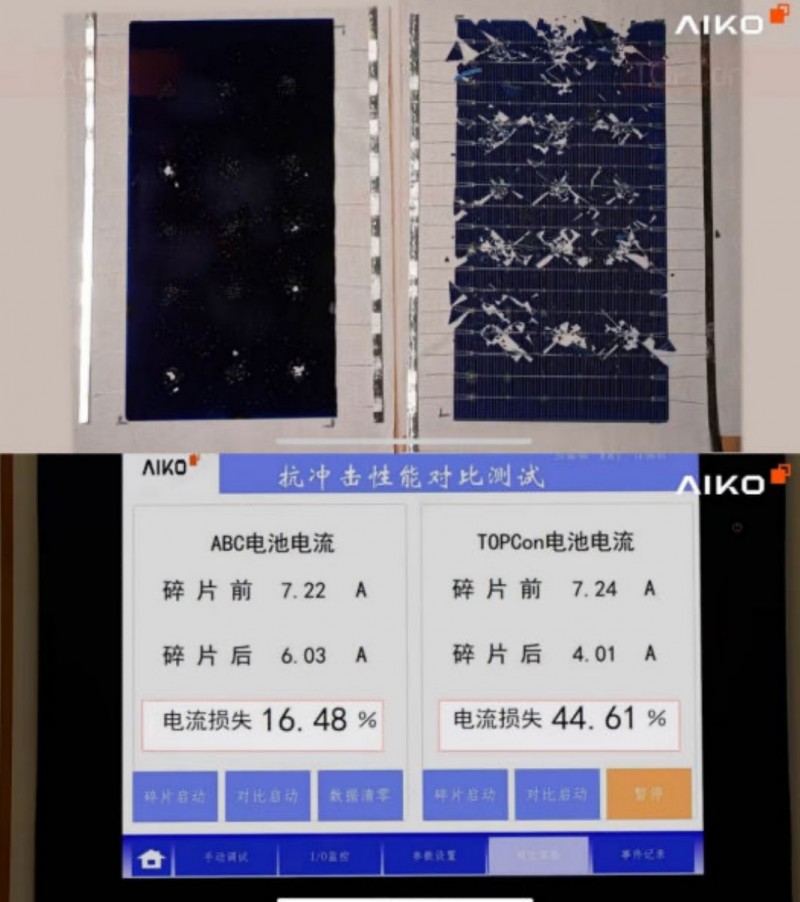
图1:抗冲击性能对比测试
近年来极端天气频发,暴雨、暴雪、冰雹……为了模拟各种意外灾害的影响,爱旭检测中心采用机械载荷实验设备,模拟极端情况下的应用场景。模拟风雪实验后的EL拍摄结果显示,爱旭N型ABC组件载荷衰减和裂片率皆小于0.5%,裂片率远低于传统组件,电池弯曲强度高于传统电池20%以上。
.jpg)
图2:机械载荷试验后组件性能对比
隐裂的风险贯穿光伏组件由生产到运行的各个环节,组件的“生命”安全离不开产业链各方共同保障,需要平稳运输、规范安装、科学运维,但最为关键的因素,仍是光伏组件自身的素质。“打铁还需自身硬”,持续提升技术工艺,向市场提供更加高效、稳定、可靠的产品,用每块组件的过硬品质为客户创造更高投资价值,是光伏制造商赢得市场青睐的必由之路。