在P型硅太阳能电池中,转换效率最高的是德国哈梅林太阳能研究所(ISFH)开发的POLO电池,达到了26.1%。作为一种交错背接触电池,POLO电池也采用多晶硅氧化层(POLO)技术实现钝化接触,并且达到了极高的开路电压(726.6mV)。
此外,采用钝化接触的主流电池结构还包括硅基异质结电池(HJT),该结构通过非晶硅实现钝化。日本钟化集团(Kaneka)将交错背接触结构和异质结技术相结合,取得了目前晶硅太阳能电池转换效率的世界纪录,达到了26.63%。
非晶硅与多晶硅之间的主要区别在于:非晶硅在加工过程中无法承受高温,而多晶硅则可以。因此,多晶硅工艺整合会相对容易,而不用被迫改变后端金属化制程。
金属化是TOPCon结构实现商业化的关键要素之一。目前,在实验室设备中,通过物理气相沉积(PVD)技术实现了全背金属接触,但该技术并不适用于大规模量产。为了将这一前景广阔的高效技术商业化,找到合适的采用丝网印刷和烧结金属化工艺的解决方案至关重要,这也引起了业界的浓厚兴趣。
此外,多晶硅还可用于构建不同的高效电池结构:N型多晶硅可取代N+扩散层,用于N型双面电池的背面;P型多晶硅可用于P型电池的背面(作为p-PERC的替代方案),从而取代铝背场电池或用作N型背结电池。相较目前的扩散层,这两种方法均可显著降低复合速率。
贺利氏积极探索可用于多晶硅层接触并最大程度地降低金属诱导复合速率的金属化浆料。这是一项具有挑战性的任务,主要原因如下:首先,由于金属-半导体相互作用的属性,降低金属诱导复合速率的要求非常苛刻。其次,对浆料的接触性能起着重要作用的多晶硅层具有显著的差别。影响多晶硅表面浆料性能的关键因素包括:
1.多晶硅的厚度
从吸收率的角度来看,优选超薄多晶硅层,但其金属诱导损失更加严重。在丝网印刷和烧结金属化工艺中,较厚的多晶硅层通常更有优势。只要多晶硅层位于电池背面,即使膜层稍微厚点,也完全可以接受。
2.多晶硅层的掺杂浓度
为了使金属和多晶硅之间形成良好的接触,必须达到足够的掺杂浓度。不管多晶硅层是在沉积时进行原位掺杂,还是在沉积之后进行易位掺杂,表面电阻率都可作为有效的度量指标。多晶硅层的典型表面电阻率高于传统的扩散层,但通常只有超薄多晶硅层才能做到这点。
3.表面形态
用于多晶硅沉积的衬底表面既可以是经过制绒的,也可以是光滑的。近期研究表明,两种类型的表面均具有出色的J0。
4.耐高温性
如前所述,能够承受较高温度是多晶硅的优势之一。但是,多晶硅层表面的金属诱导复合速率也是温度函数,通常随着温度升高而加快。
5.多晶硅层的均匀性
多晶硅层的均匀性通常随厚度增加而提高。这对于接触性能有一定的影响,因为不均匀的多晶硅层容易在金属化过程中遭受更严重的局部损坏。
以下是贺利氏浆料与多晶硅层接触的部分结果。图1对比了三种浆料(分别标为浆料1、2和3)在薄多晶硅层和厚多晶硅层表面的接触电阻率。
浆料2在薄多晶硅层和厚多晶硅层表面的性能较为相似。另一方面,浆料1在厚多晶硅层表面的性能最为优异,其接触电阻率只稍高于当前浆料(参照物)在扩散发射极表面的接触电阻率。浆料3在厚多晶硅层表面的接触电阻率也更低。
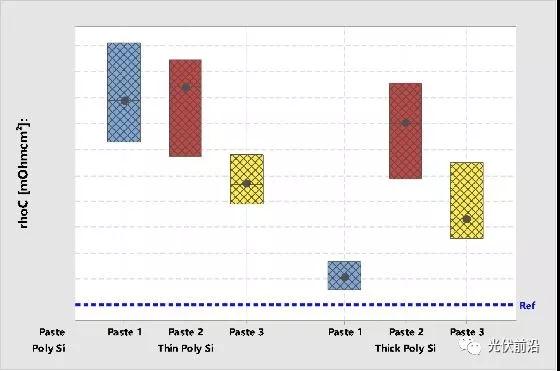
图1:贺利氏浆料1、2和3在薄多晶硅层和厚多晶硅层表面的接触电阻。浆料1在厚多晶硅层表面的性能最为优异
通常来说,当烧结温度较低时,多晶硅能够更好地保留钝化特性。因此,在足够低的温度下,为多晶硅接触而开发的金属化浆料应该也能够形成低电阻接触。图2显示了改进后浆料在高烧结温度和低烧结温度下的接触电阻率。
一开始,浆料A在高烧结温度下具有良好的接触电阻率,但在低烧结温度下,接触电阻率显著升高。在开发过程中,浆料A经改进后得到的浆料A1和A2在低烧结温度下的性能有所改善。以传统扩散发射极表面的丝网印刷与烧结浆料的接触电阻作为参照,在低烧结温度下,浆料A2在多晶硅表面的接触电阻与参照电阻相近。
与制绒表面相比,光滑表面的多晶硅层的J0通常较低。但从多晶硅沉积工艺的近期发展来看,光滑表面与制绒表面的J0已经不分伯仲。不过,这两种类型的表面的接触性能会有所不同。图3显示,不同表面类型所适合的浆料也有所不同。浆料A在制绒表面的接触电阻率与参照电阻接近,但在光滑表面则很高。浆料B恰好相反,在制绒表面的接触电阻率要优于光滑表面。
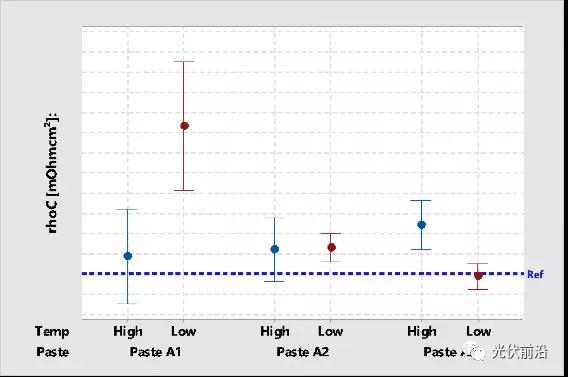
图2:随着技术发展,浆料在多晶硅层表面的接触电阻率进一步提高,浆料A3在低烧结温度下表现出了出色的接触电阻。
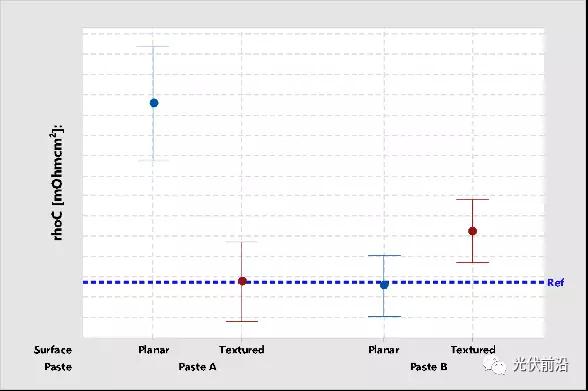
图3:不同硅片表面的浆料接触电阻率对比
毋庸置疑,多晶硅的特性对于浆料特性具有深刻的影响。通过与行业合作伙伴及研究机构通力合作,贺利氏在开发多晶硅层接触用丝网印刷浆料方面取得了重大进展。针对不同类型的多晶硅层,贺利氏开发出了接触电阻最优并且能够最大程度地降低金属诱导复合速率的金属化浆料。我们始终秉持着“百尺竿头,更进一步”的态度,精益求精,致力于不断降低金属诱导复合速率,以最终实现真正的具有低接触电阻的钝化金属接触。